◆ Kamaka Factory Tour ◆ asofoct2016
|
Kamaka's factory and offices are located 15minute walk from the center of down town. They look a bit more compact than imagined. The followings are photos taken during my visit. |
|
|
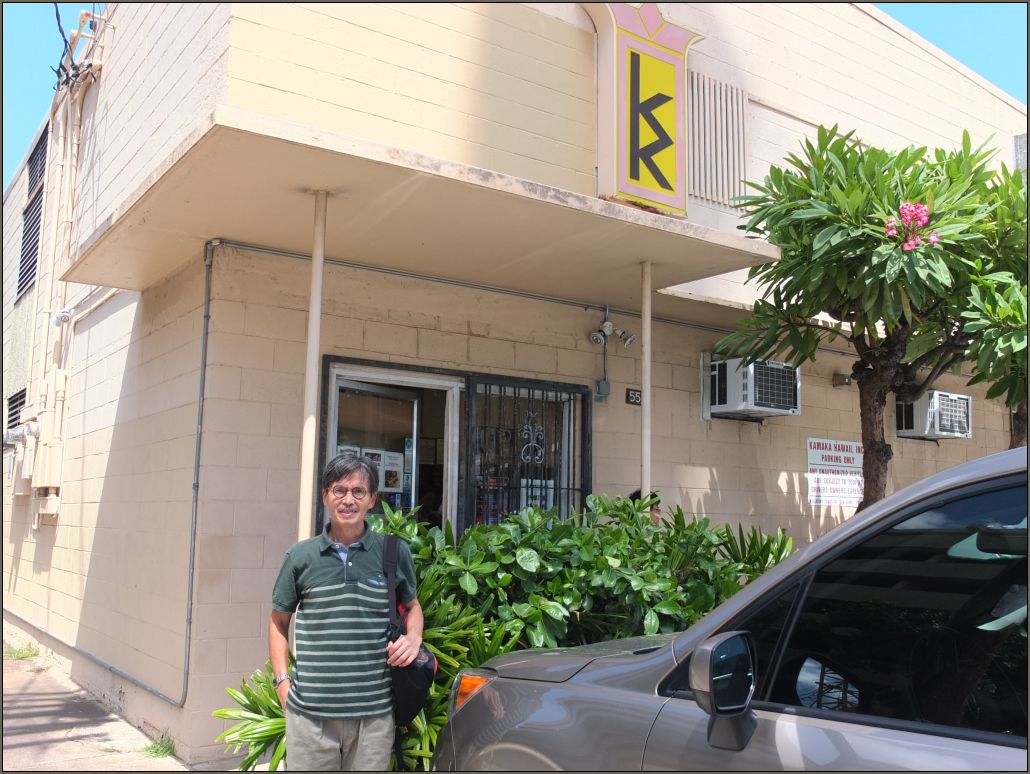
|
|
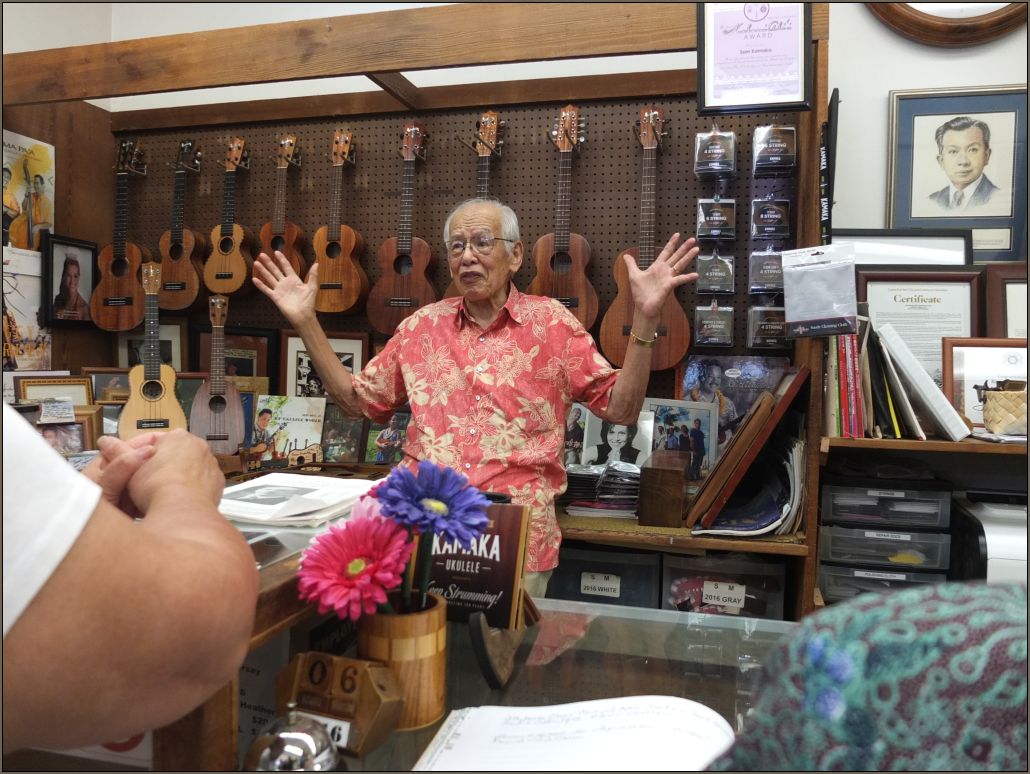 |
|
The tour started with a lecture by son of the founder, which continued more than 30 min talking on their history. This year Kamaka celebtrates 100th anniversary of the founding.
He delivered speech, along with his personal stories, on specific events over 100 years including the World Depression, WW 2, Korean war he served, etc. He took a pineapple-shaped ukulele on his hand which was first introduced by him and became the best seller. He also demonstrated to prove that the quality and the volume of the sound are not connected with a shape of the body.
In the middle of his talk there happened a surprise among us when he mentioned his age of 92 years and his elder brother aged 94. Kamaka's logo, double K, came from the initial of two brothers and Kamaka's credit was also established by them.
|
|
|
|
After 30+ min of lecture by Mr. Kamaka, we were guided by grandson of the founder(3rd generation). He walked us to the warehouse behind the office, where a variety of wood materials were being stored. |
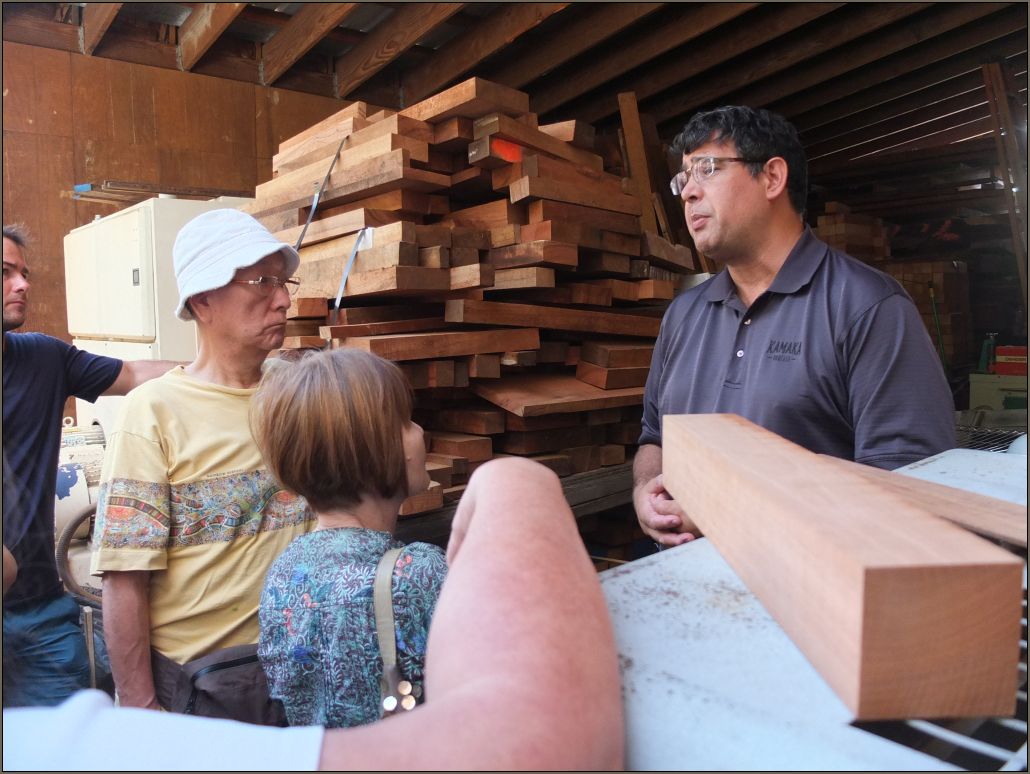 |
|
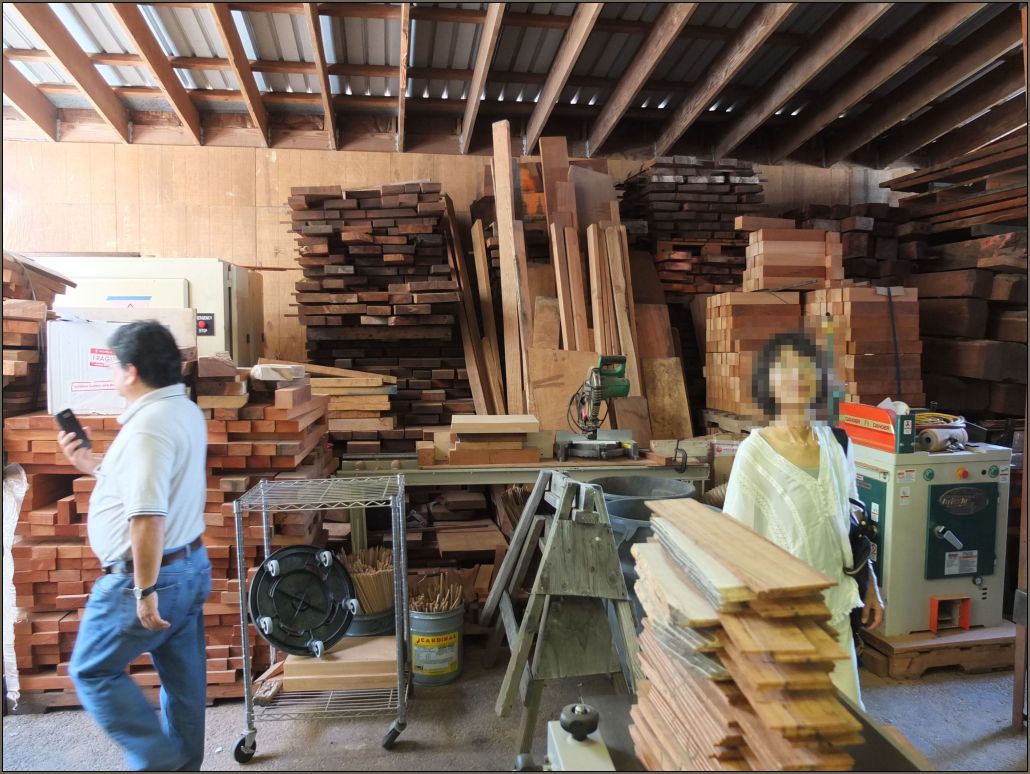 |
|
|
|
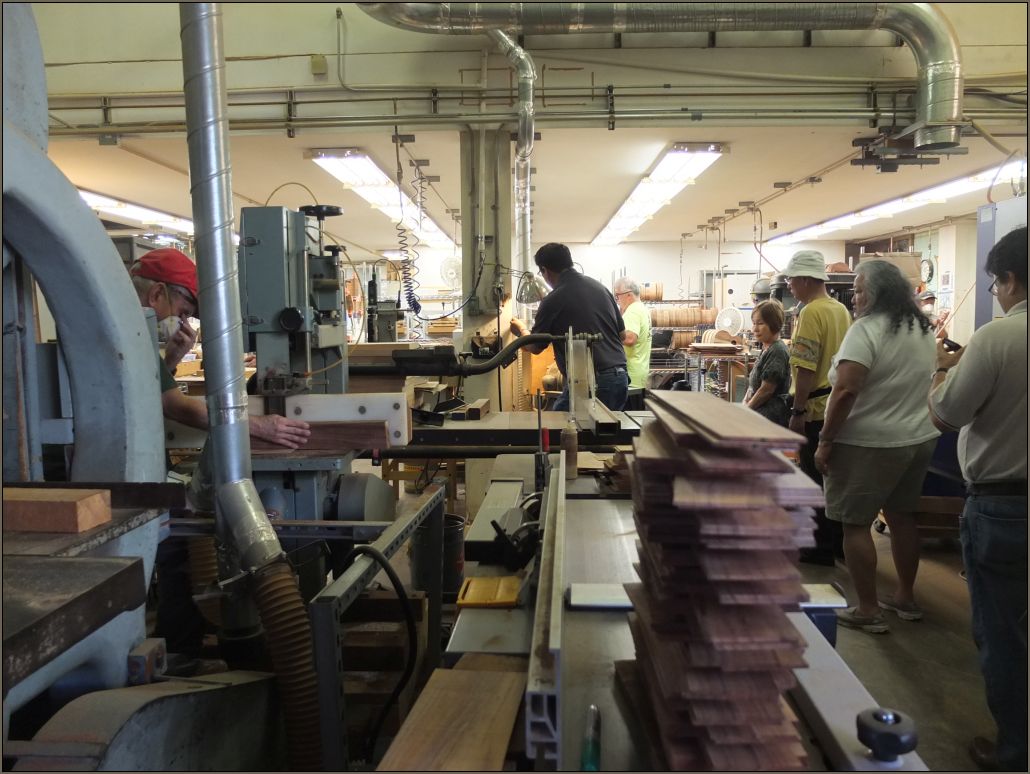 |
|
Inside factory view from the storage area. |
|
|
|
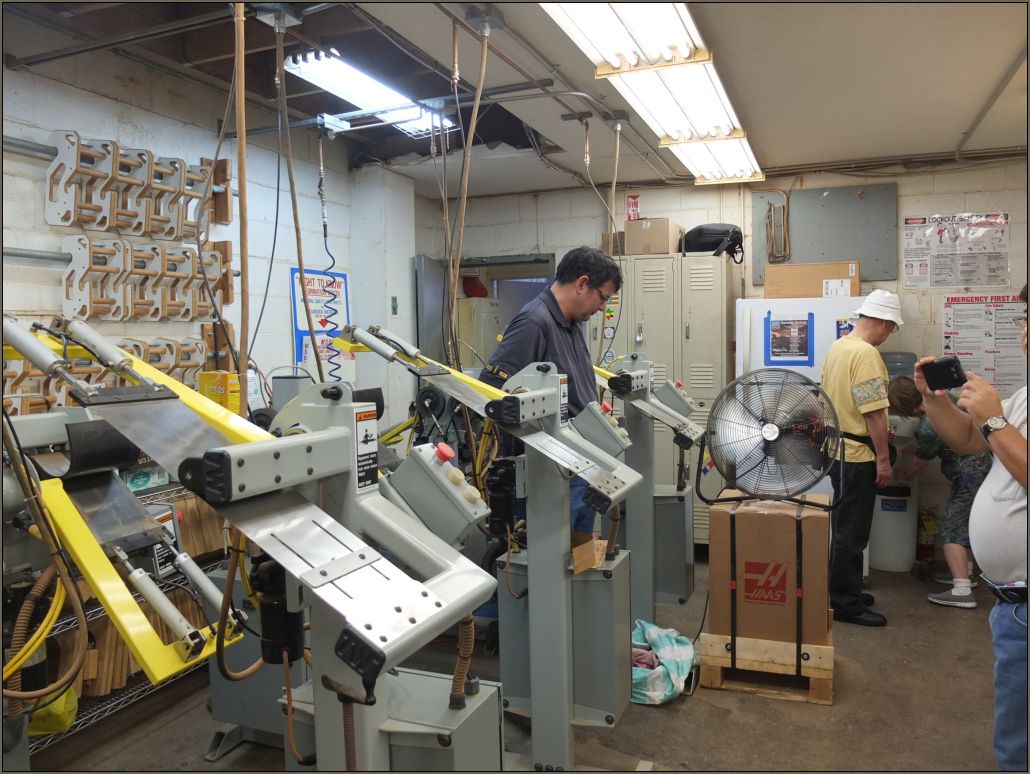 |
|
This is the place for the bending work of side materials.
There are three big machines to bend the waist of the side, then goes to next equipment for final bending (See PIC below right).
|
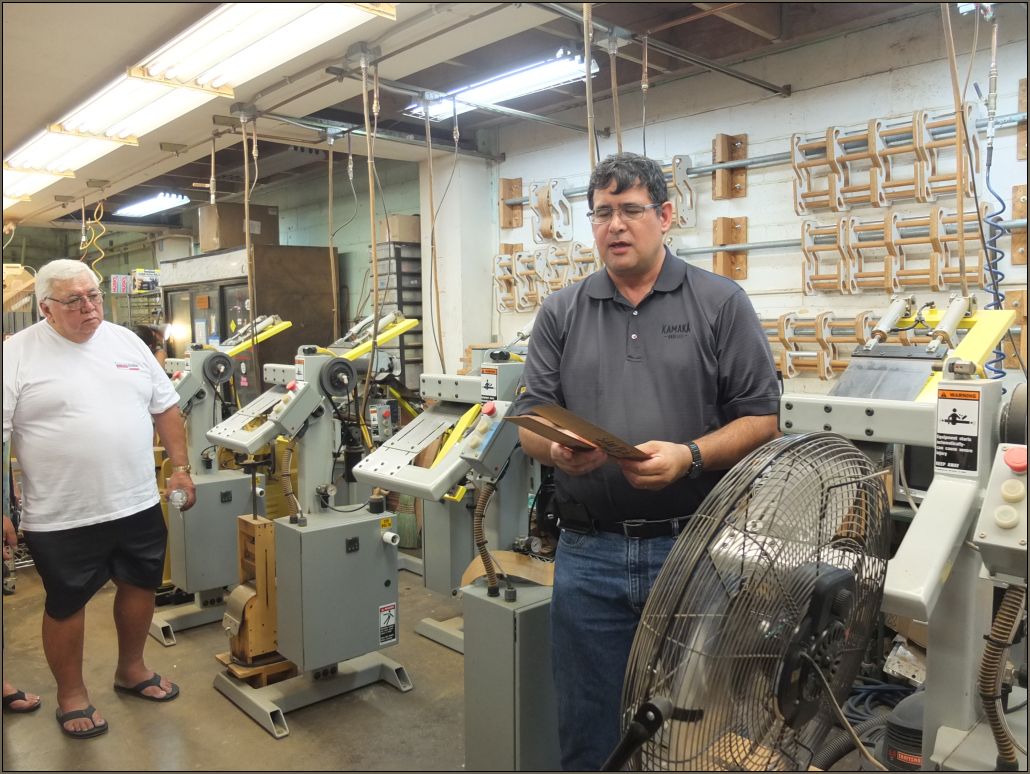 |
|
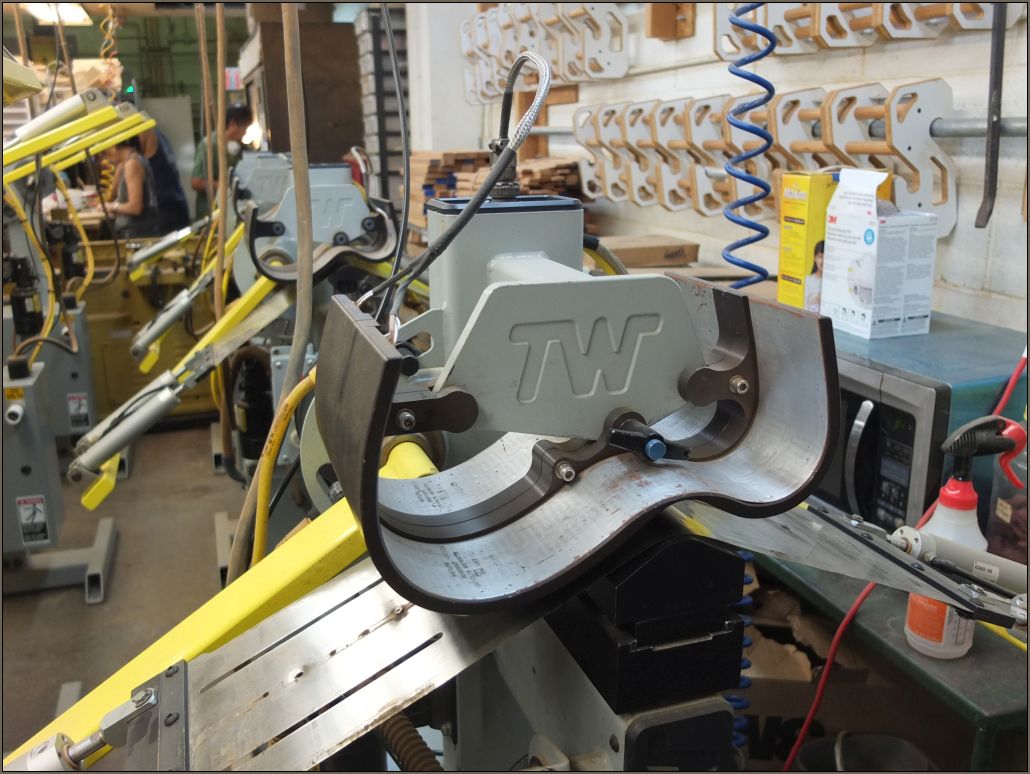 |
|
|
|
PIC below left shows gluing the linning or kerfings to the side. PIC below right shows jointing two pieces of boards into one piece of board. PIC bottom left is drying machine for the top and backboard. Last PIC shows the process of gluing the braces to the board. It was almost the time for staff to take lunch break. |
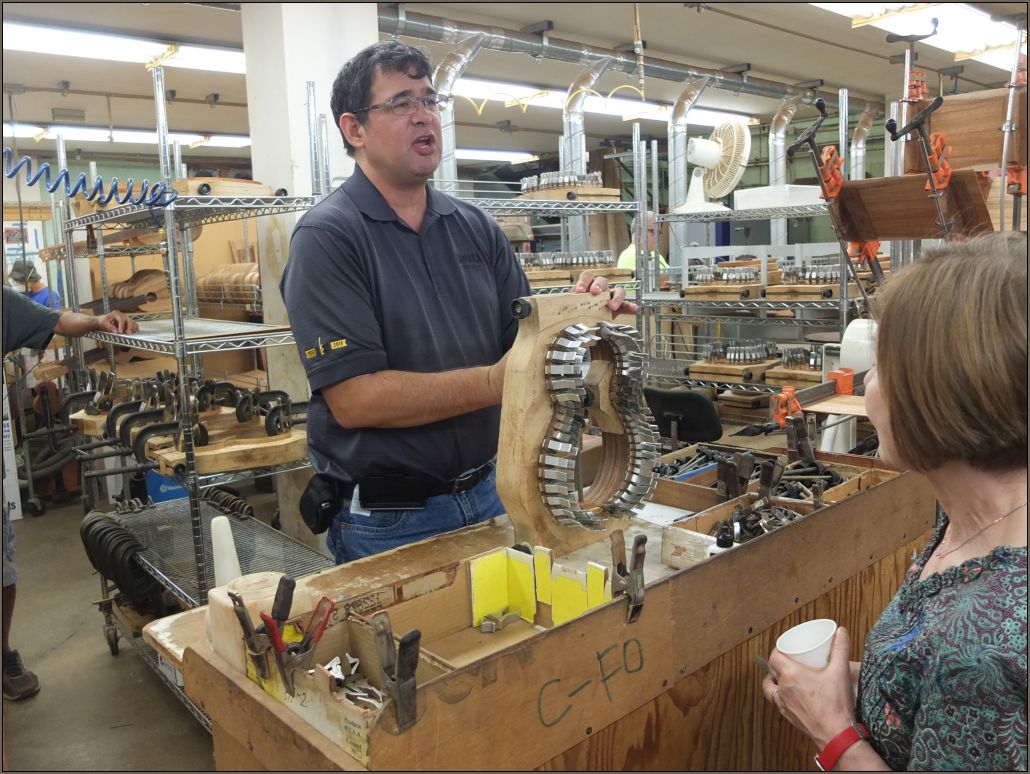 |
|
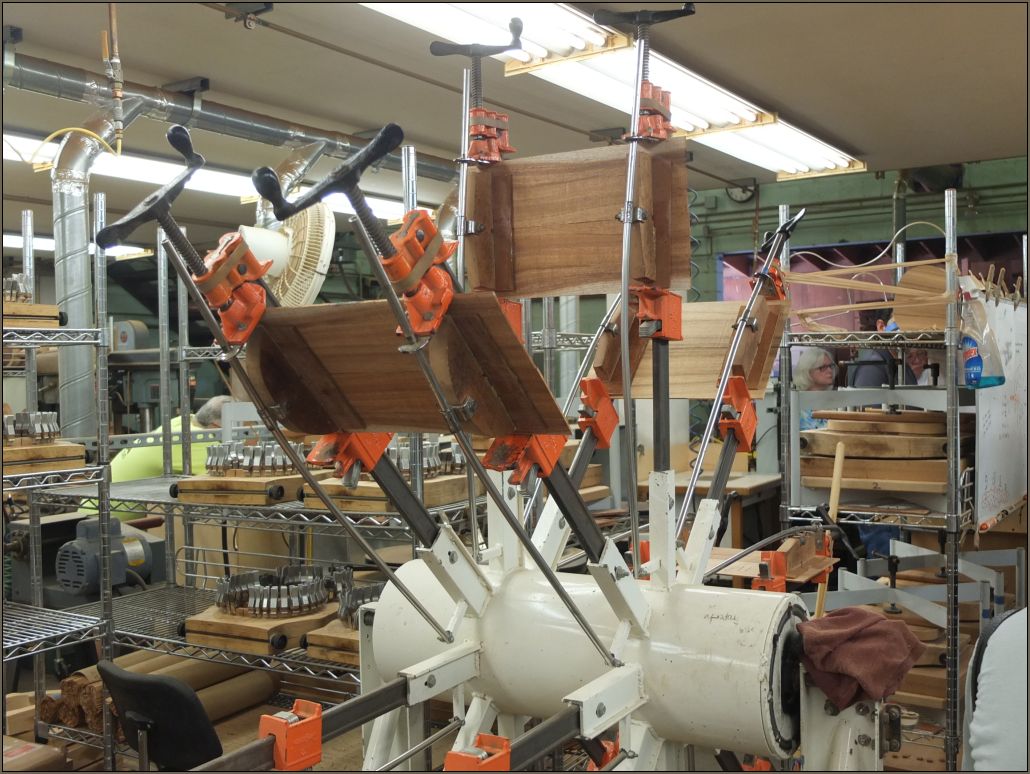 |
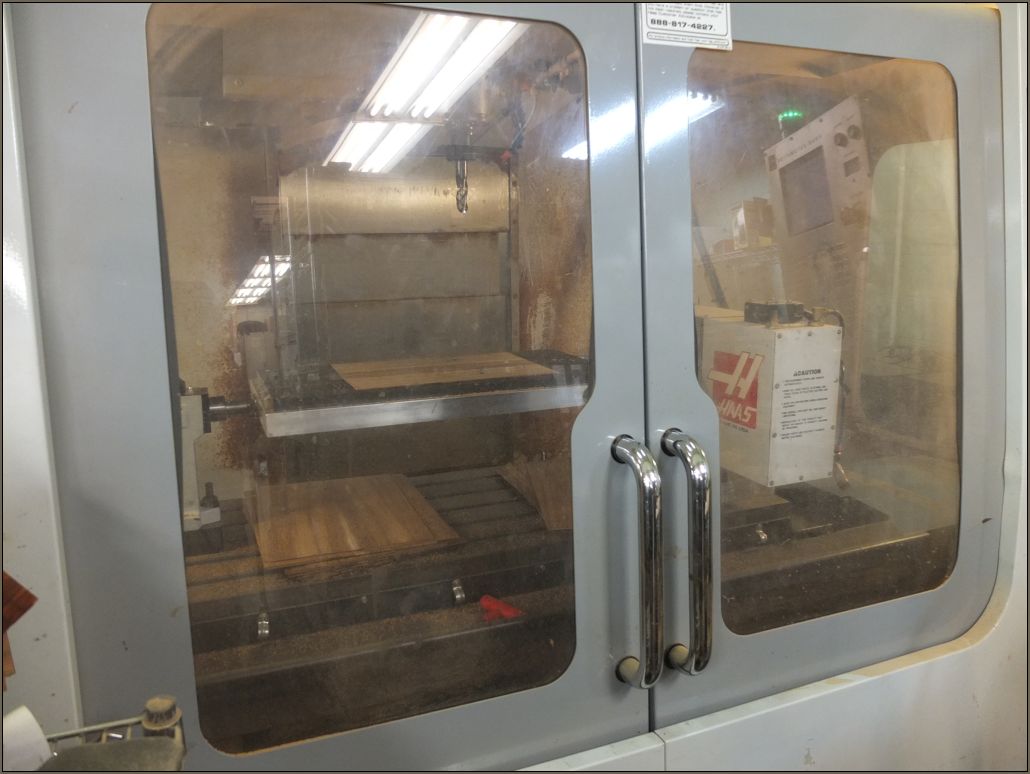 |
|
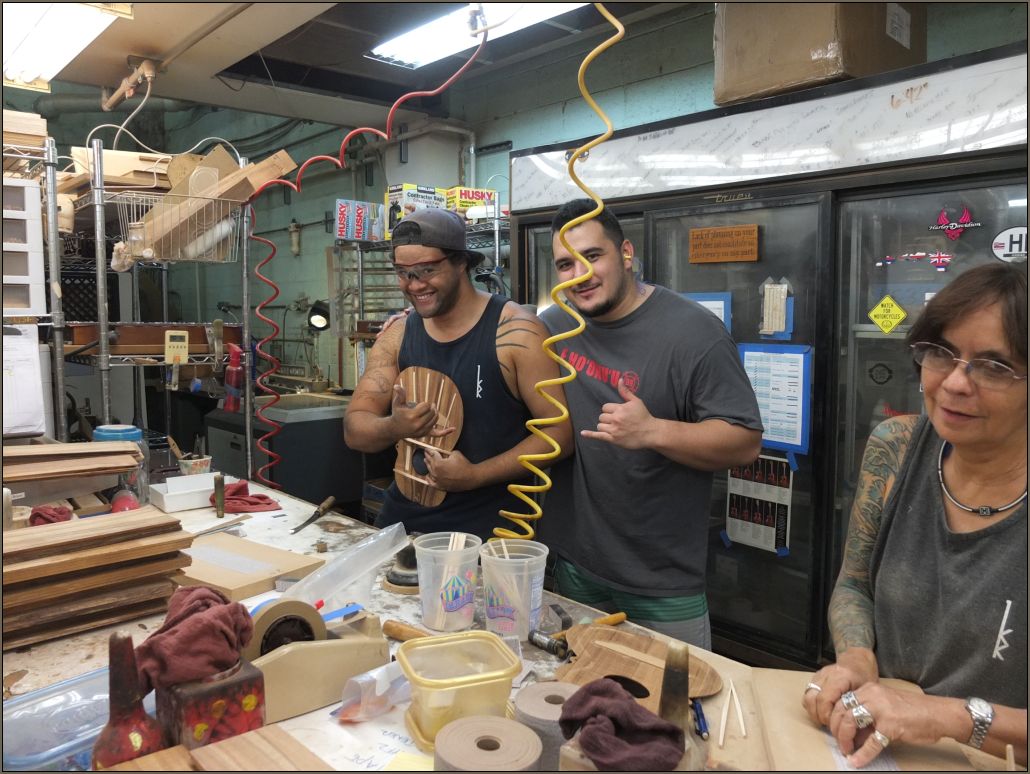 |
|
|
|
He was explainning the usage of the mold which creates the body shape, and dove tail joint of neck and body. Every work, needless to say, was being processed by using specific tools that could avoid even small errors.
There are several sanding devices behind him, circled in red. One is used to sand the body surface flat and the other one has a concave surface to make the backboard surface round. |
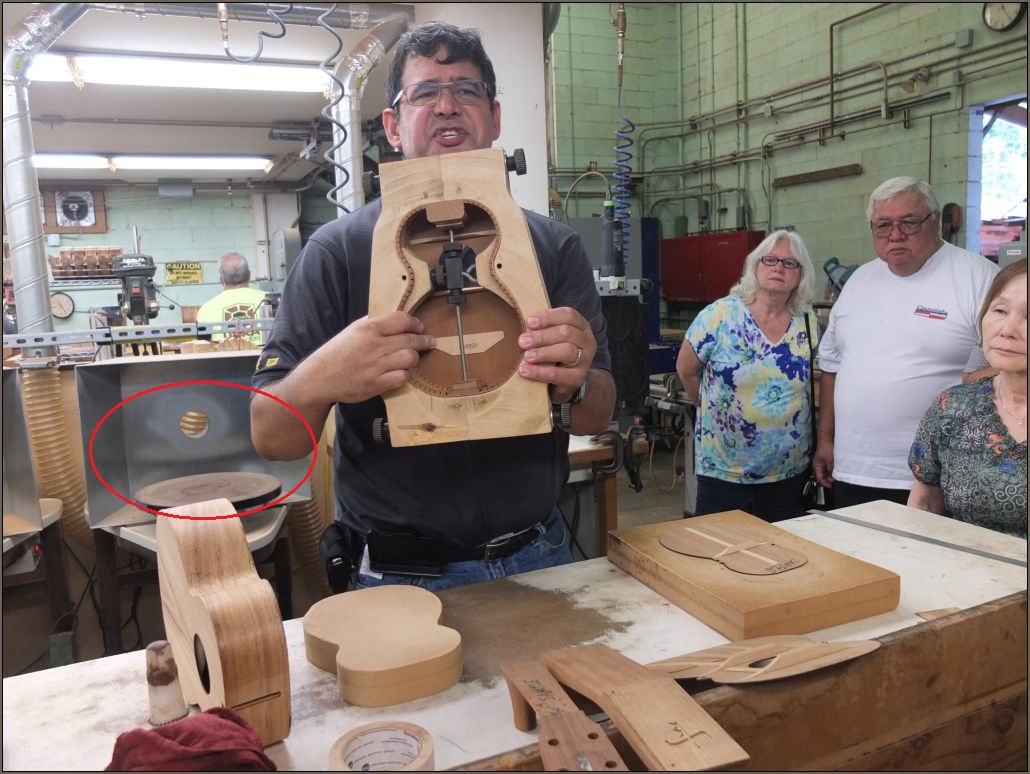 |
|
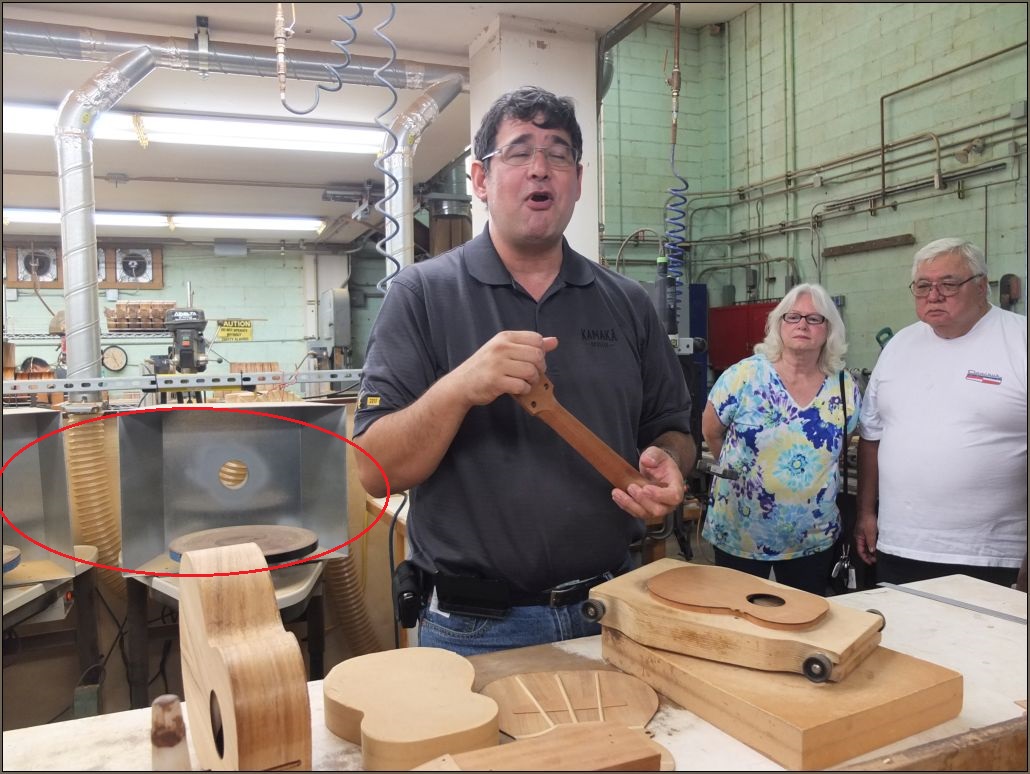 |
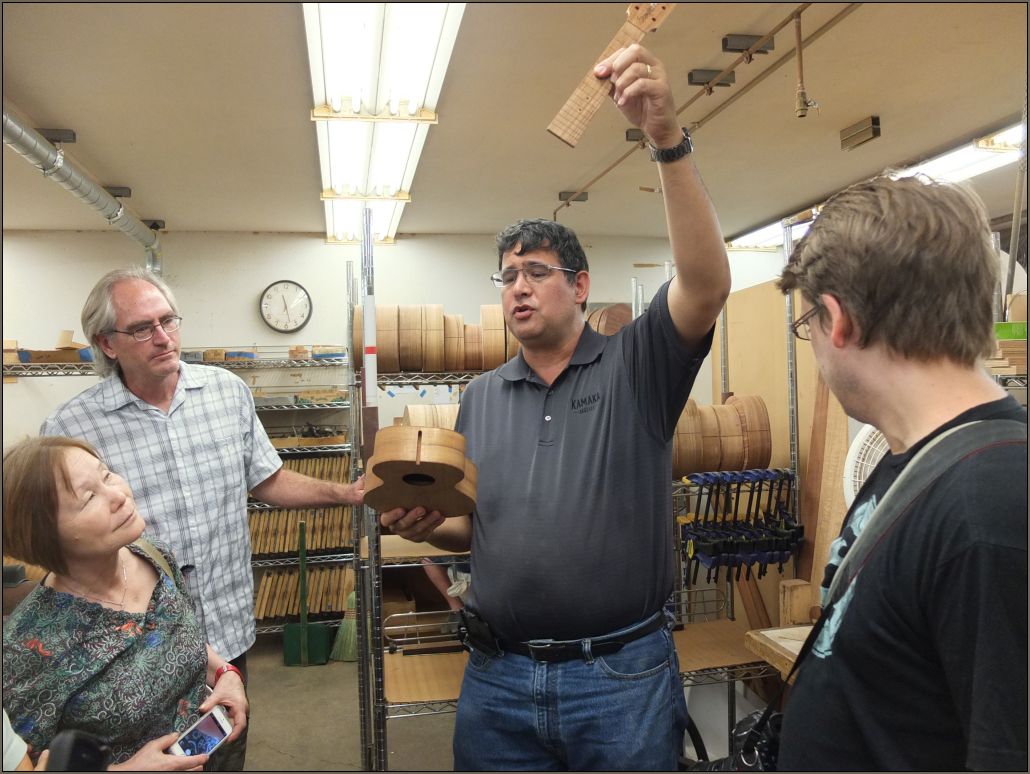 |
|
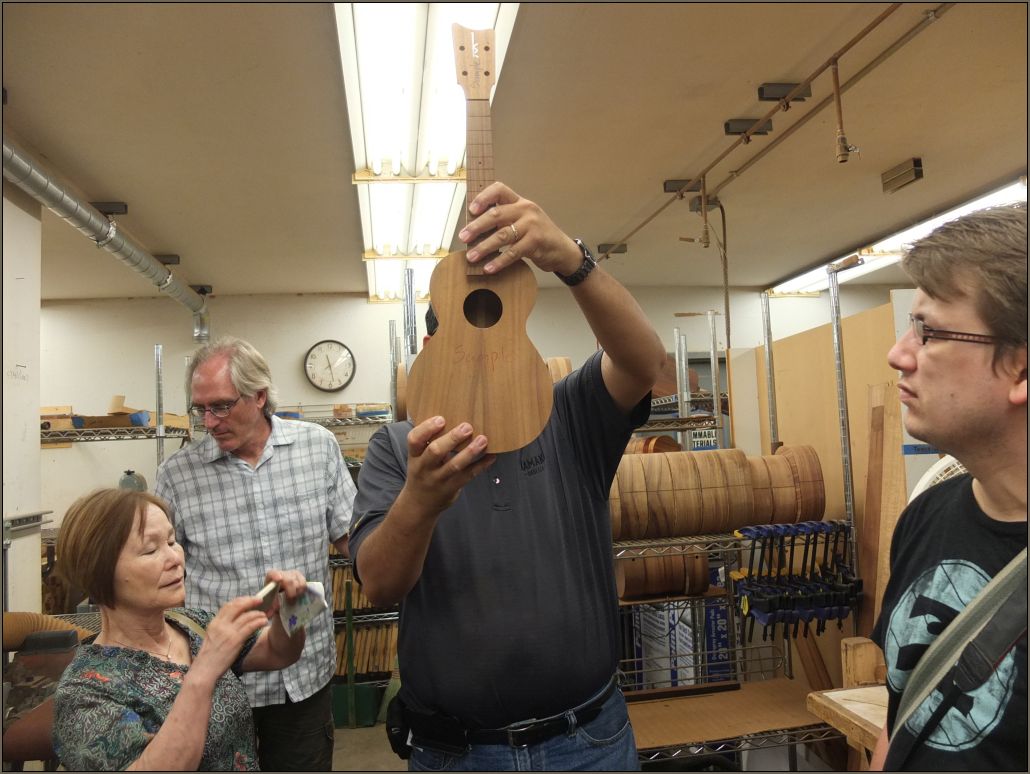 |
|
|
|
Storage bin, you could see headstock inlay of 100th anniversary.
At present they have several months of backorder and last shipment will be scheduled on January 2017.
|
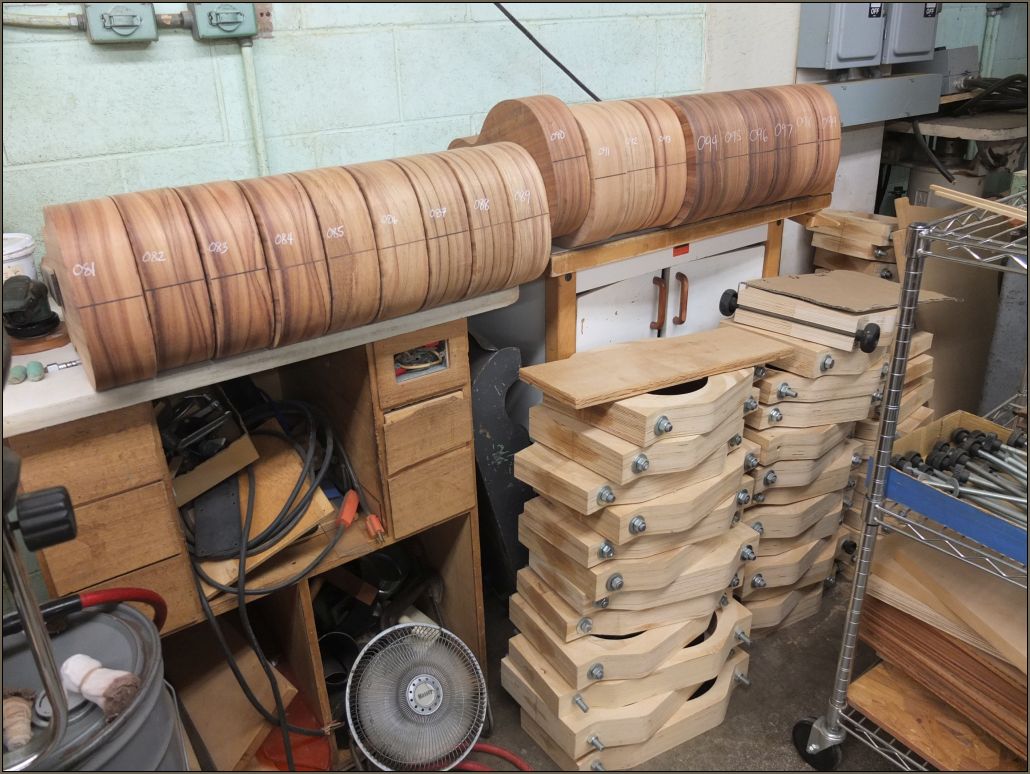 |
|
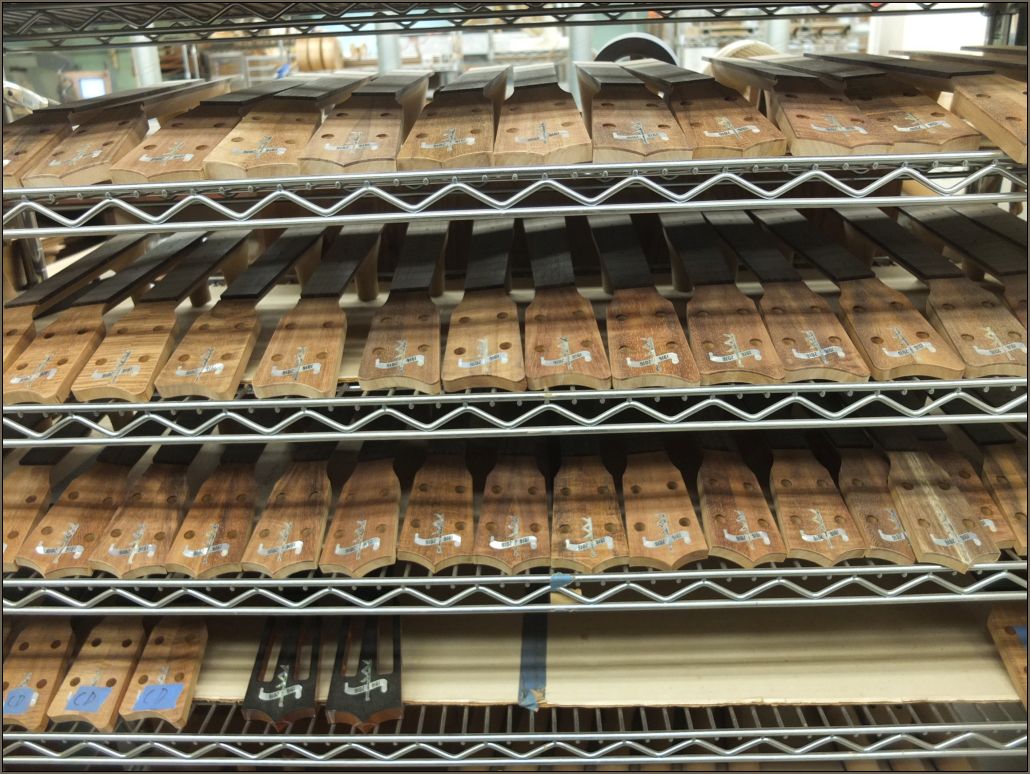 |
|
|
|
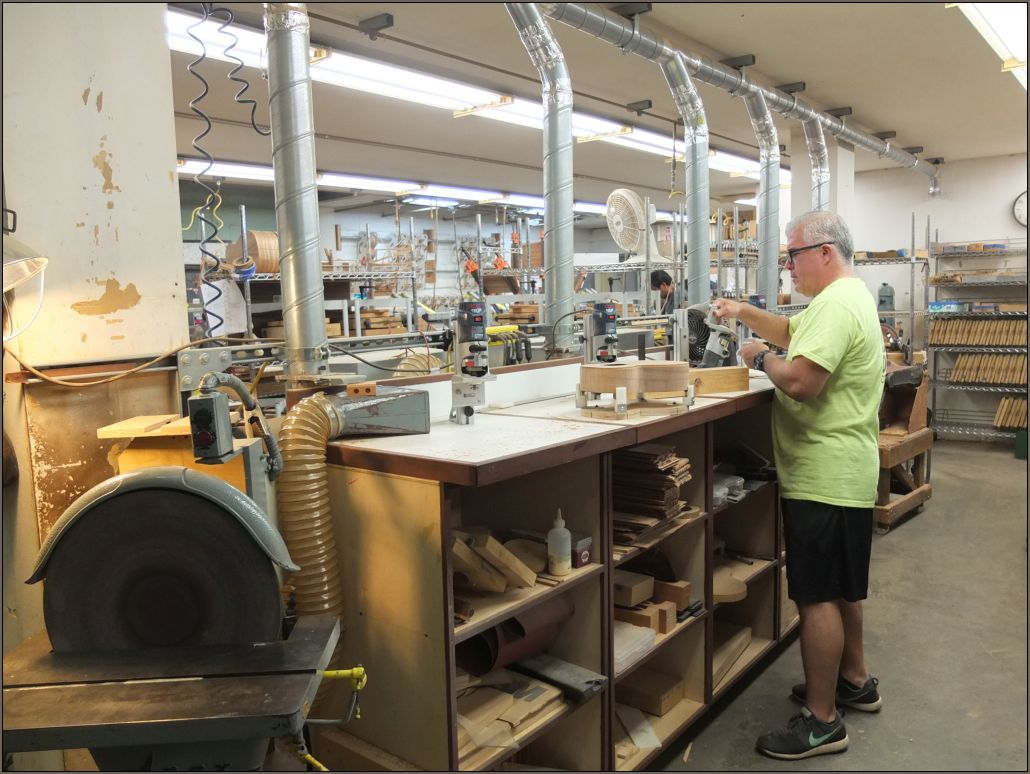 |
|
Three routing tools, for the process of binding work, head stock inlay and the like. |
|
|
|
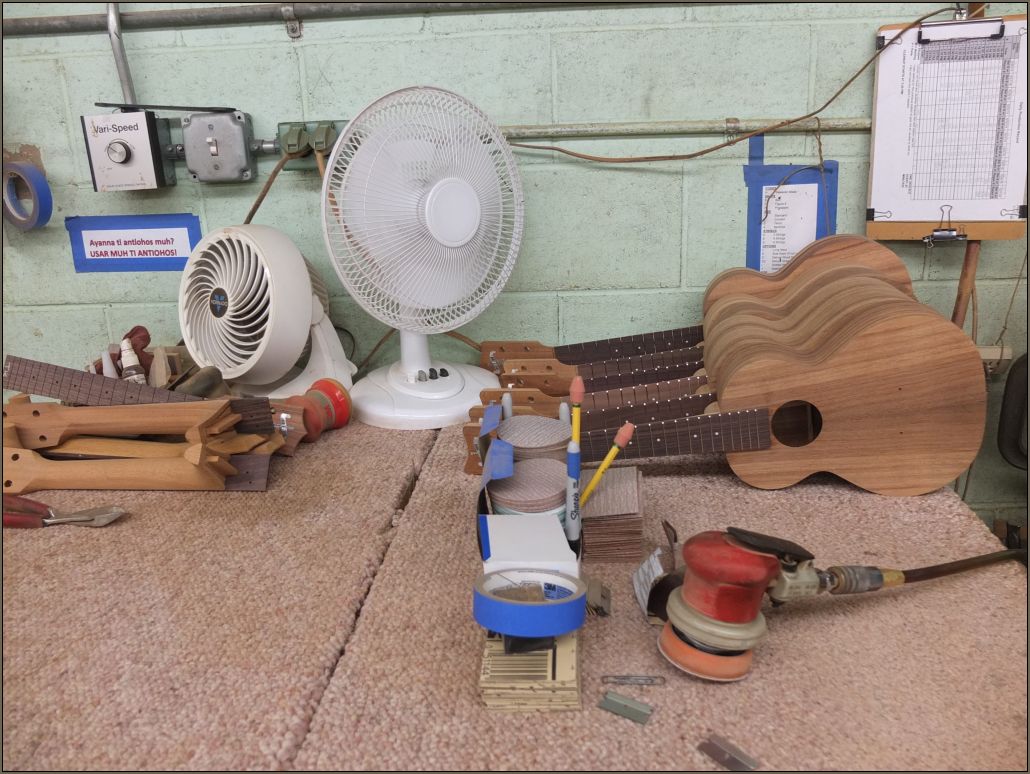 |
|
PIC left : Sanding process after fingerboard is attached.
PIC below : Masking the fingerboard and bridge before painting, Desktop is totally covered with artificial leather to keep ukulele flawless.
PIC bottom, drying process after top coating.
|
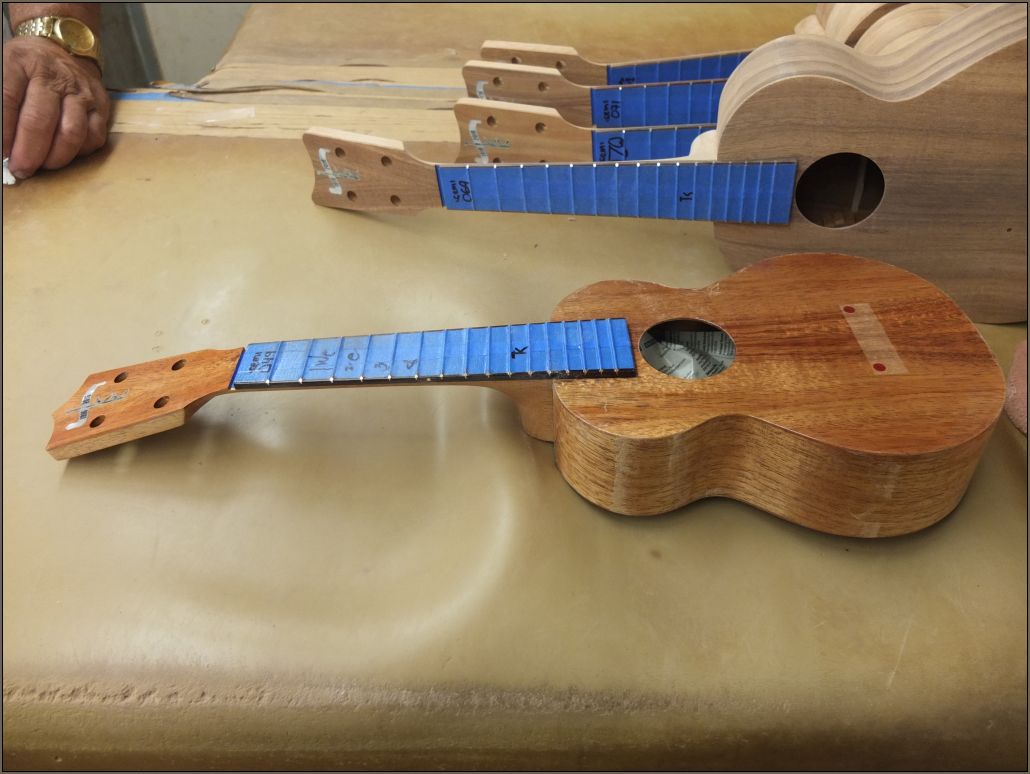 |
|
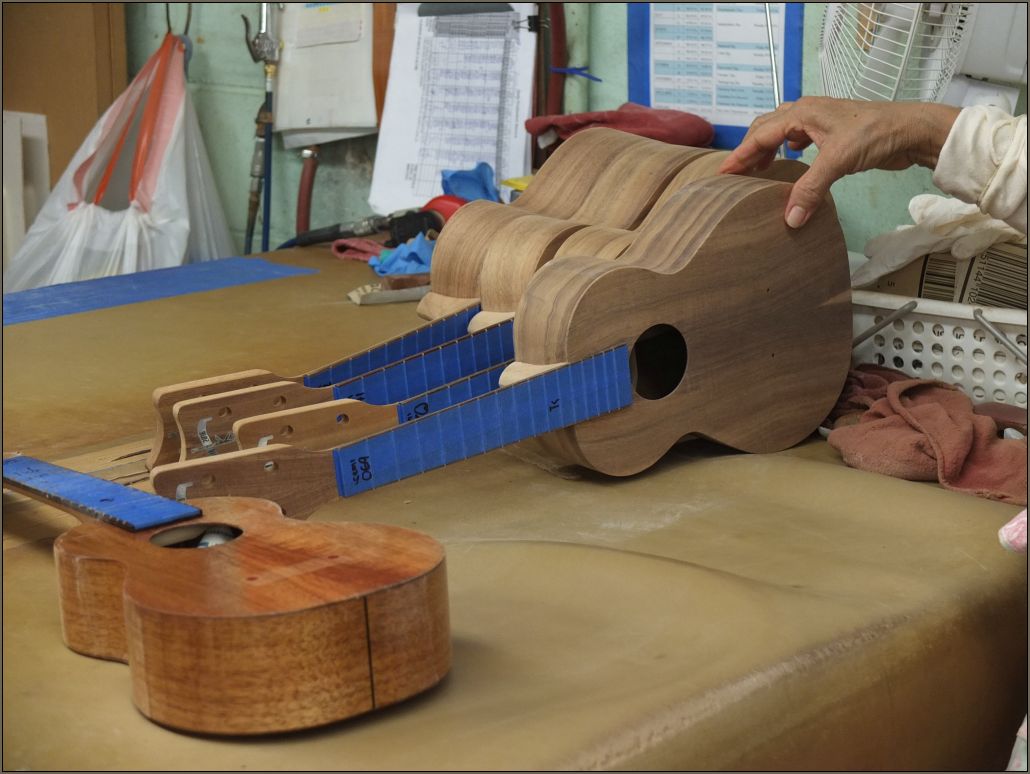 |
|
|
|
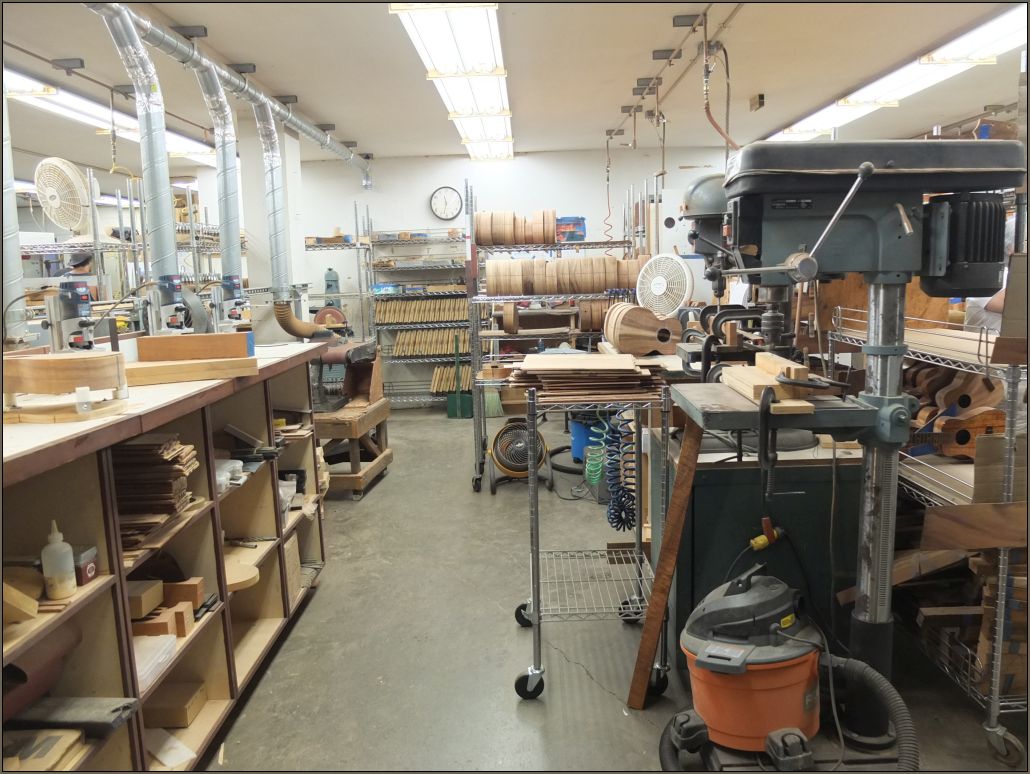 |
|
Summary of work process;
1. Binding and Inlay
2. Joint neck and body
3. Glue the fingerboard to the neck
4. top coating and drying
|
|
|
|
Final work at 2nd floor. We were moving upward. |
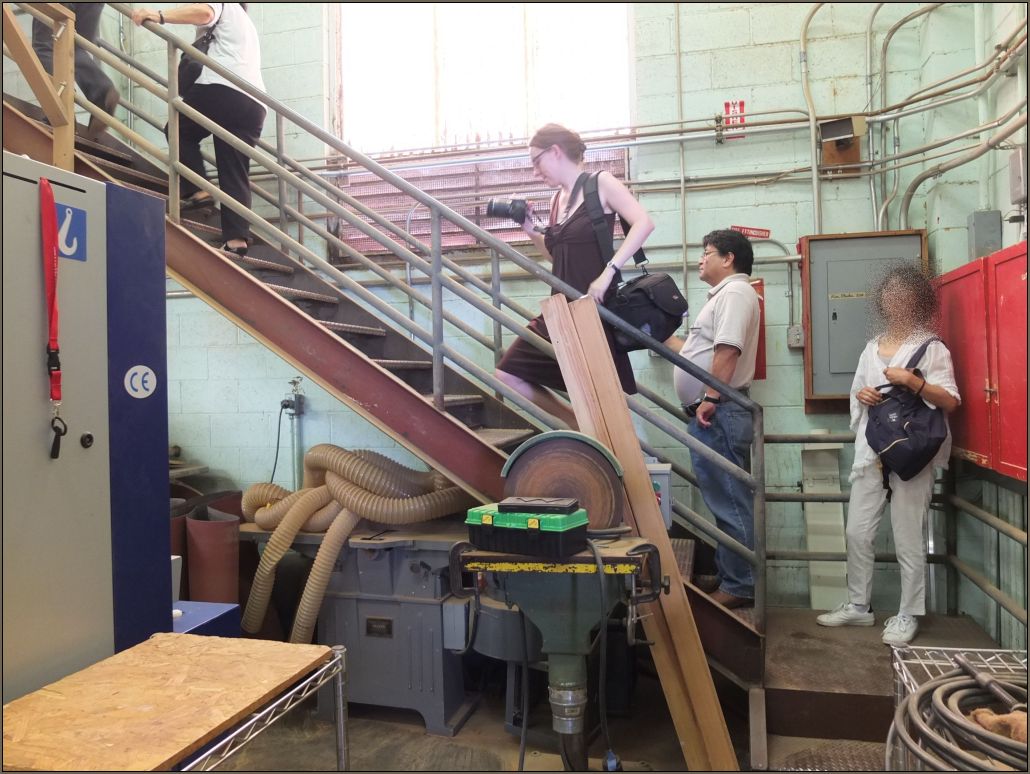 |
|
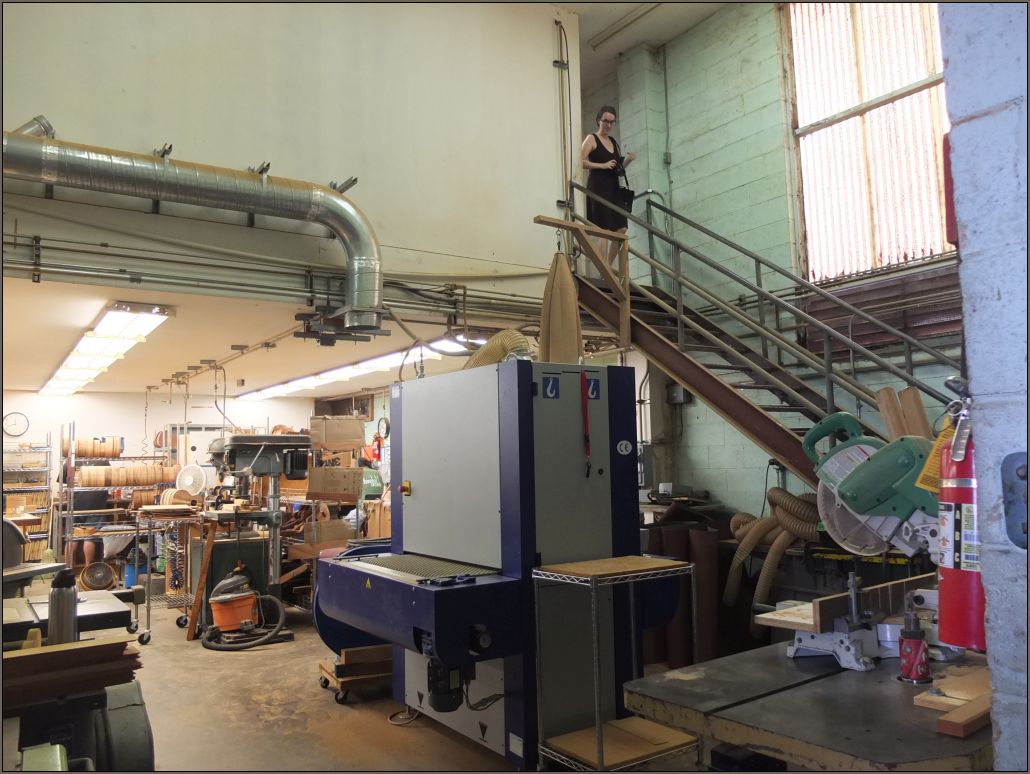 |
|
|
|
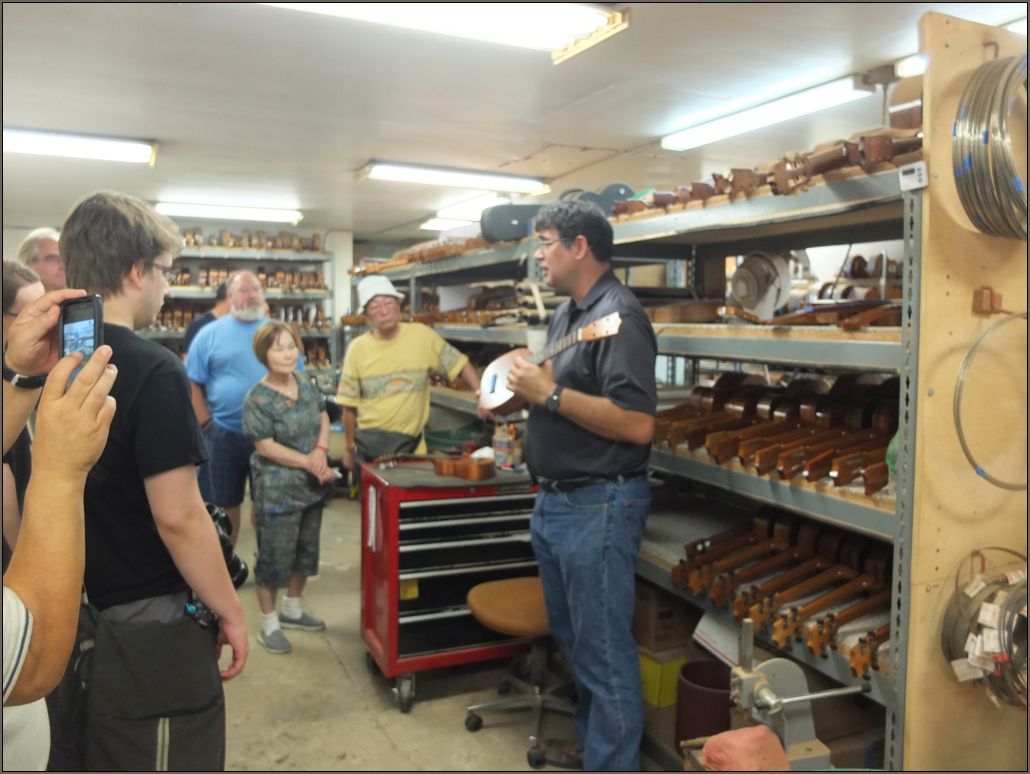 |
|
Final process : Tuning machine, saddle and bridge are to be fixed, and strings fitting as well.
Today they are producing roughly 15 pieces of uklele a day. I felt they would'nt expand their business even in the future and maintain the scope of business at this level.
Kamaka's standard model is priced at $995. It surely is reasonable, isn't it? I'd like to have it someday.
Now, two brothers are fairly sharing management all over manufacturing to marketting. This family business would be going the right way and the future will be O.K as well.
|
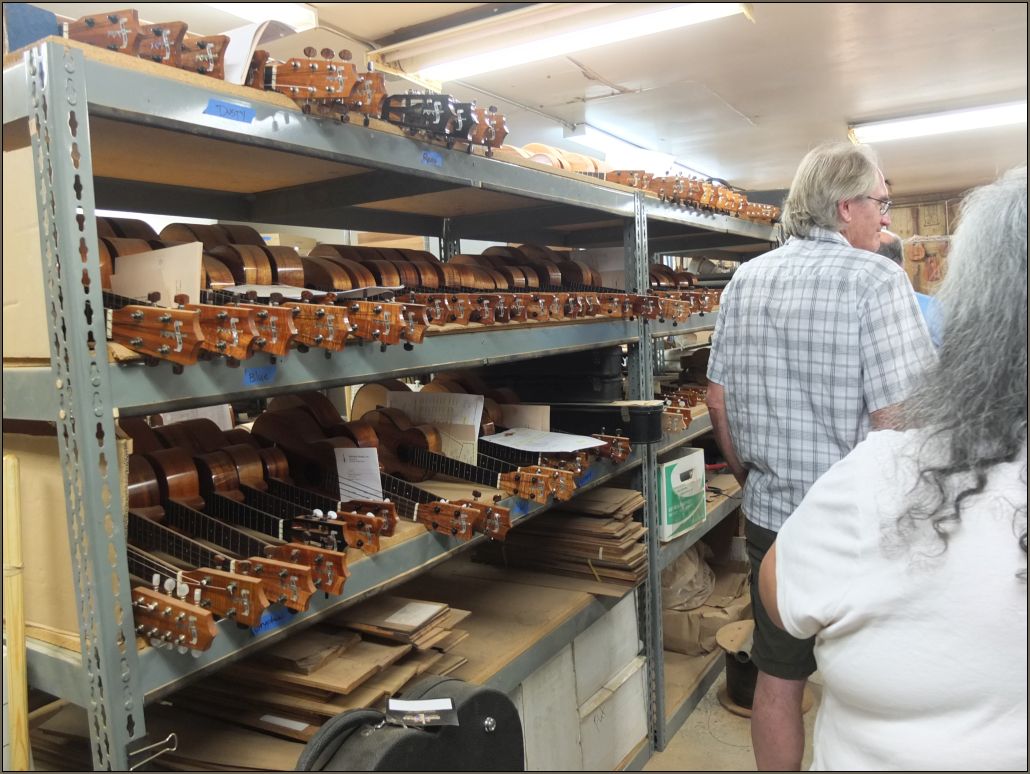 |
|
|
|
|
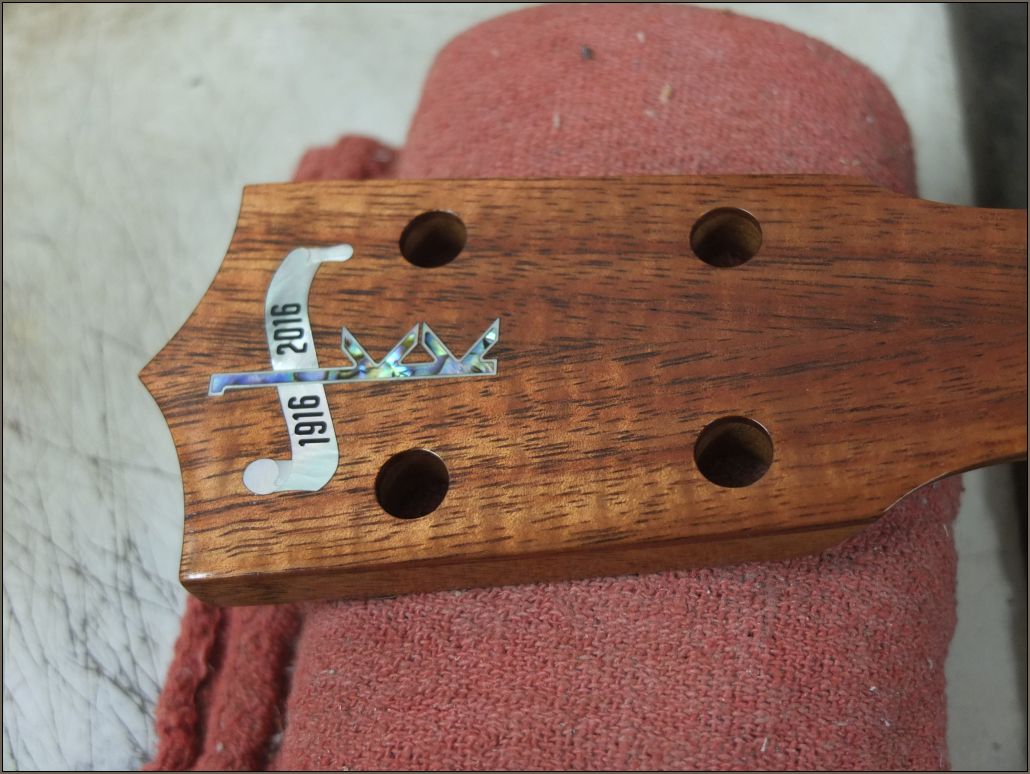 |
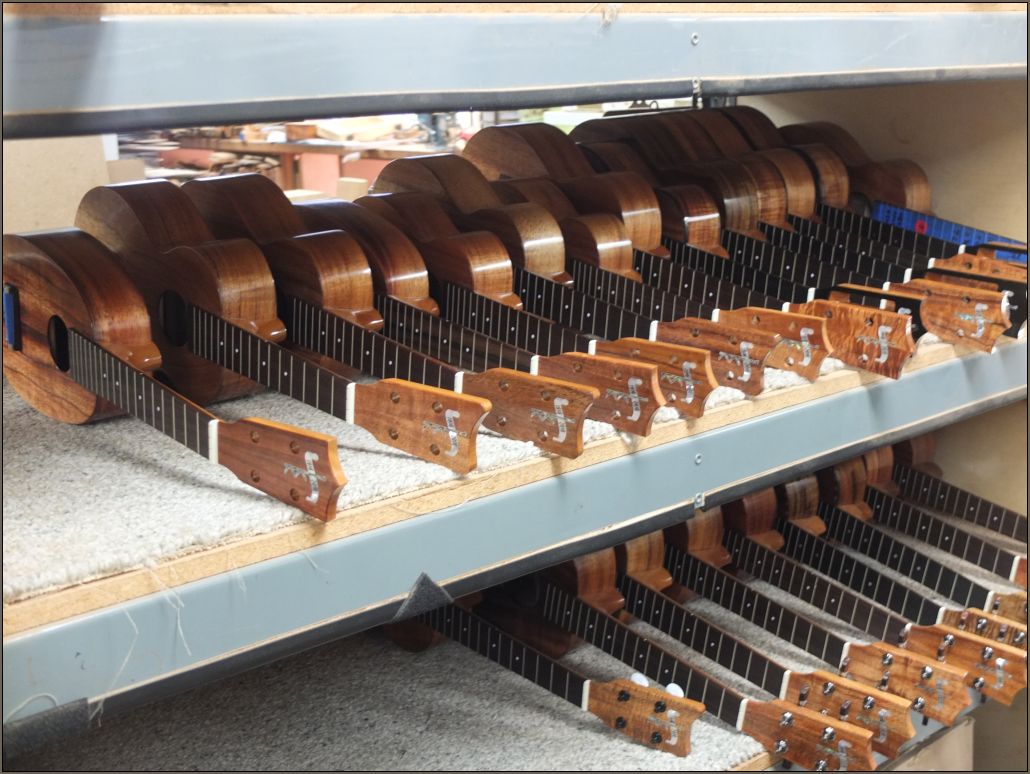 |
|
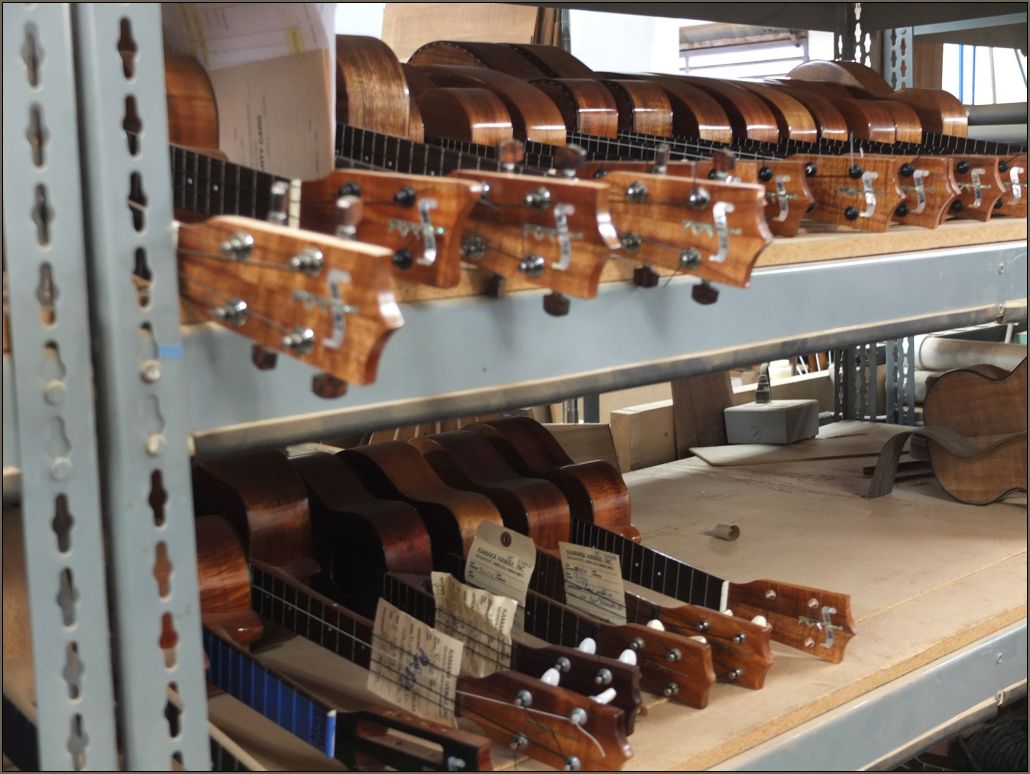 |
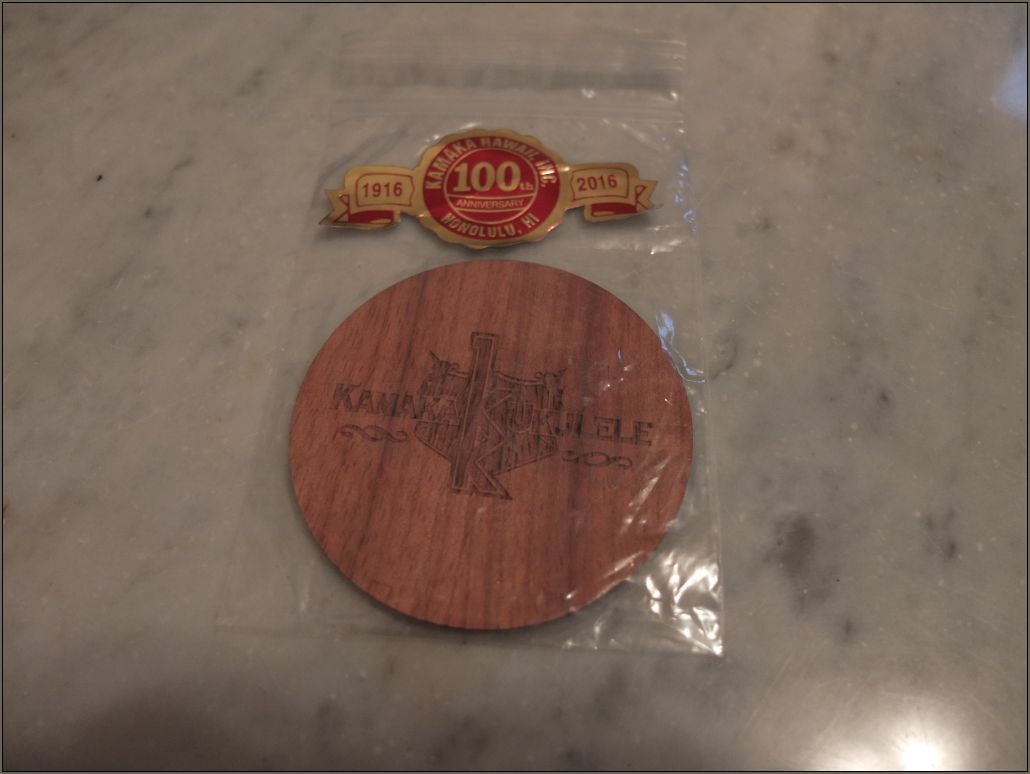 |
|
Souvenir was given to all of us.
An anniversary seal is impressed on it. This has been produced as a sort of scraps of sound hole work. |